Chain Restaurant
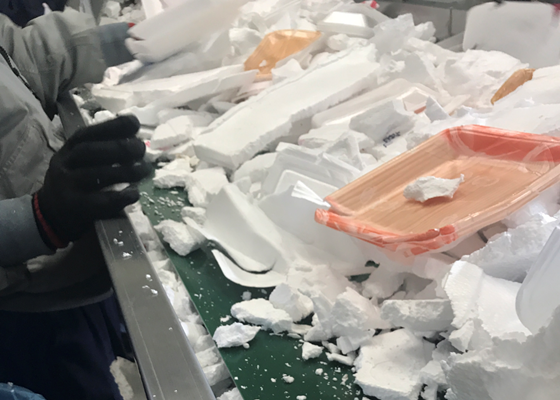
For example, Walmart logistics distribution centers in the U.S. generate a large amount of foam packaging, waste cardboard, waste plastic film, etc. GREENMAX has a waste management solution specifically for retail supermarkets. The foam volume reduction machine can solve the problem of waste foam disposal. For the recycling of waste paper and plastic film, GREENMAX provides vertical or horizontal balers to hydraulically compress and pack materials to improve the warehousing turnover efficiency of retail supermarkets.
Wal-Mart is a chain super enterprise with many branches in the United States and even around the world. GREENMAX has reached a cooperation with the Walmart Return Center in South Carolina, USA, to provide it with its foam recycling solution.
Foam takes up a lot of space in warehouses and is very expensive to transport. Walmart is one of the most environmentally conscious companies, so they pay more attention to professionalism when choosing a foam recycling machine. After fully understanding the professionalism of GREENMAX, the South Carolina Walmart Return Center finally decided to purchase a GREENMAX foam densifier M-C100.
GREENMAX first had an in-depth understanding of Walmart's foam recycling needs, including foam density, output and other indicators. GREENMAX then designed a waste foam recycling solution that best suits Walmart's needs. The GREENMAX foam densifier is now running smoothly in the Walmart factory with a compression ratio of 90:1, helping them solve the problem of foam waste disposal and reduce the area occupied by foam.
Meanwhile, GREENMAX baler is also widely used in major supermarkets, which is an equipment specially designed for compressing and baling various wastes, including horizontal and vertical series. This machine is mainly used for recycling the cans, PET bottles and oil tanks. It can compress waste materials into compact bales and reduce the volume of waste plastic. The machine is highly automated and can save labor costs. A large amount of waste plastic is put into the feeding bin and compressed into tight plastic bales, saving storage space and transportation costs. After cleaning, these plastic bales can be made into plastic pellets, which are the raw materials for recycled plastic products.